由于SiC硬度大和易脆裂等特性,晶錠切割成為制約SiC器件制造核心瓶頸。近期,日本Dry Chemicals開(kāi)發(fā)了一種新的工藝,能夠?qū)iC晶圓的制造成本降低20~30%。
該技術(shù)的核心是在晶錠上進(jìn)行開(kāi)槽,這樣可以使得晶圓切片的時(shí)候更加平整,從而減少晶圓表面的研磨、拋光等后處理所需的步驟數(shù)量。目前,該公司將于10月份開(kāi)始晶圓代加工,并且對(duì)外銷(xiāo)售該設(shè)備,預(yù)計(jì)第一年銷(xiāo)售5~10臺(tái)。
該技術(shù)的步驟主要是在切割前,先用磨石在晶錠要切割的位置開(kāi)出一個(gè)圓周凹槽,這些凹槽可以充當(dāng)線鋸的導(dǎo)向裝置,從而可以更精確地切割晶片。
由于SiC晶體特別堅(jiān)硬,在切割的時(shí)候會(huì)發(fā)生漂移,如果有凹槽,磨??梢杂行У貪B透,從而很難發(fā)生漂移,這種方法能夠?qū)⒕A表面的損傷控制在最小限度。對(duì)于厚度為15mm的晶錠、可以切割20個(gè)凹槽,目前該工藝所能切割的最大晶錠厚度為40mm,可以切割75片晶圓。
一般情況下,對(duì)晶錠切割后需要對(duì)晶圓的端面進(jìn)行加工刮平,但基于這項(xiàng)工藝的晶錠切割,會(huì)直接形成刮平,進(jìn)一步提高了效率。只需要在切割后立即進(jìn)行鏡面研磨、化學(xué)機(jī)械拋光(CMP)、清潔和檢查即可獲得成品。
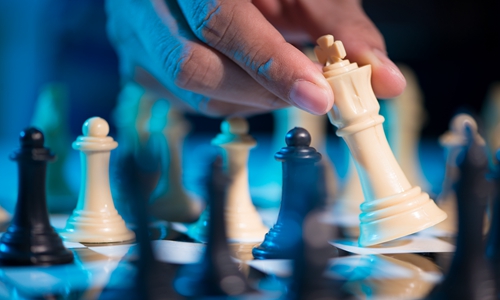
圖片來(lái)源:拍信網(wǎng)正版圖庫(kù)
SiC切割
為了提高良率,近年來(lái)不少企業(yè)都采用更為先進(jìn)的激光切割和冷分離技術(shù)。
其中英飛凌通過(guò)收購(gòu)一家名為SILTECTRA的科技公司,掌握了SiC的冷切割技術(shù),該切割技術(shù)主要分為2個(gè)技術(shù)環(huán)節(jié)。首先是用激光照射晶錠剝落層,使SiC材料內(nèi)部體積膨脹,從而產(chǎn)生拉伸盈利,形成一層非常窄的微裂紋。第二步則是通過(guò)聚合物冷卻步驟將微裂紋處理為一個(gè)主裂紋,最終將晶圓與剩余晶錠分來(lái)。該技術(shù)能夠?qū)⒉牧蠐p失降到最低,并且讓單個(gè)晶錠可出產(chǎn)的芯片數(shù)量翻番。
在激光切割SiC這一領(lǐng)域,國(guó)內(nèi)也有企業(yè)正在探索。今年5月,德龍激光表示其已經(jīng)布局SiC晶錠切割,已經(jīng)將6英寸的加工時(shí)間縮短至15分鐘以內(nèi),且分片后研磨損耗小于 50 微米,在總體時(shí)間上,德龍激光的一錠切出來(lái)30片晶圓,大概需要4~5個(gè)小時(shí),相對(duì)于傳統(tǒng)的金剛線則只能切出22、23片晶圓來(lái)說(shuō),激光切割效率提升了40%左右,目前德龍激光的最大可切割尺寸為8英寸。
(文:集邦化合物半導(dǎo)體Jump整理)
更多SiC和GaN的市場(chǎng)資訊,請(qǐng)關(guān)注微信公眾賬號(hào):集邦化合物半導(dǎo)體。